190T full lining Single layer tugboat bag XJ-TB116D
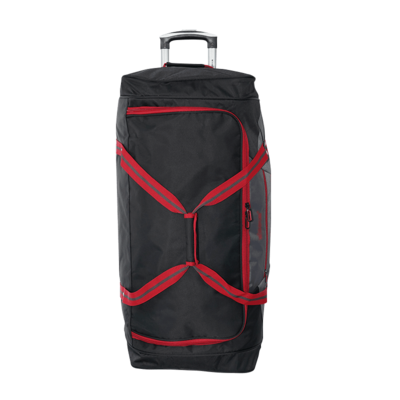
190T Full Lining Single Layer Tugboat Bag XJ-TB116D is a high quality, absolutely waterproof packing bag, which can be used for shipping and receiving goods in outdoor activities.190T polyester fabric, soft and comfortable, waterproof, durable and easy to clean. Has plenty of space for storing things. The large main compartment, with a zipper waterproof bag inside, can be used to store daily necessities or personal items.190T Full Lining Single Layer Tugboat Bag. The bag is made of 190T Oxford Fabric, which is solid and durable. With great responsibility for heavy objects, the bottom is made of high density PE foam and the inside is full-lined to prevent damage to the items inside it.With a single-layer structure, this bag is a perfect choice for travelers who prefer a low-key look and travel light. The viscose, cotton and linen material provides softness and comfortable touch. While its multiple functional pockets, adjustable waist strap, dual zipper pulls make it easy to arrange your belongings.
It's also durable enough to resist dents.For most travelers, though, polycarbonate is the better choice. It's also more affordable. Besides being strong, polycarbonate is also easy to form into different shapes and sizes. It's also resistant to chemicals and temperatures.Besides being durable, polycarbonate is also transparent. It's one of the only plastics that's recyclable. It's also one of the lightest materials you can find. It's also the strongest material on the market.When comparing materials, it's important to remember that impact resistance is the key factor. If you're choosing a suitcase, you'll want something that's durable and can withstand bumps and knocks. This is why polycarbonate and ABS are commonly used in hard-sided luggage.Despite its reputation as a poor cousin of the polycarbonate family, PVC is actually quite versatile and is a worthy contender. It is not prone to dents like polycarbonate, and its lightweight properties mean it is less likely to cause baggage damage than its more robust cousin.A good way to understand its performance is to take a look at the various uses of PVC in the home and garden sector. For example, it is widely used in roofing membranes and for insulating electrical wiring. Another application is for building construction, where it is used as a replacement for traditional wood frames.
It is also widely used as anti-stone damage protection.PVC has also been used in a number of other applications including window profiles, ceiling systems, and exterior side mouldings. It is also a good choice for window insulators. Its good electrical insulation properties make it a good choice for window coverings. It can also be recycled in a more eco-friendly fashion than many of its plastic cousins.Aside from its obvious uses, PVC is also used in automobiles. It has been in commercial production for almost half a century. It is a lightweight, durable and highly versatile material, making it a viable alternative to metals such as aluminium and steel.During the Second World War, American scientists Carothers and a team of researches developed a new polyamide - Nylon 66. Nylon 66 is a highly durable and lightweight material. In addition to being strong and abrasion resistant, it is also resistant to fungi, gasoline and aromatic compounds. It is used in aircraft and aircraft parts, automobiles, and other applications.It is produced through two processes.
The first process involves the manufacture of a fibrous material. The second process involves the bonding of fibres to a matrix. The latter process is more common for commercially important materials.Both processes are characterized by high morphological homogeneity, which leads to good fatigue properties and tensile strength. The first process produces fibre preforms, often in sheets. The second process creates fibres in three-dimensional forms, resulting in fibers with a high softening point and dimensional stability.The second process is characterized by the presence of a rubber-compatible agent, which is impregnated with carbon fibers. This improves crystallite orientation in the direction of the fiber axis. The final heat treatment temperature is around 1500degC.These fibers are typically made of glass, but can also be made of polyethylene or polycarbonates. They are used in products such as backpacks and duffel bags.